Basic Info.
Product Description
The Front pane is manufactured on a 5-step-hydraulic press line. The raw material is delivery as blanks.
- Step1:conner cutting and punching;
- Step2:forming and bending;
- Step3:punching and side-punching;
- Step4:side-cutting and side-punching;
- Step5:bending;
All die bushings out material full bronze with solid lubricants inserts.
All the cutting punches and cutting knives made of material 1.2379,through-hardened (60+-2 HRC).
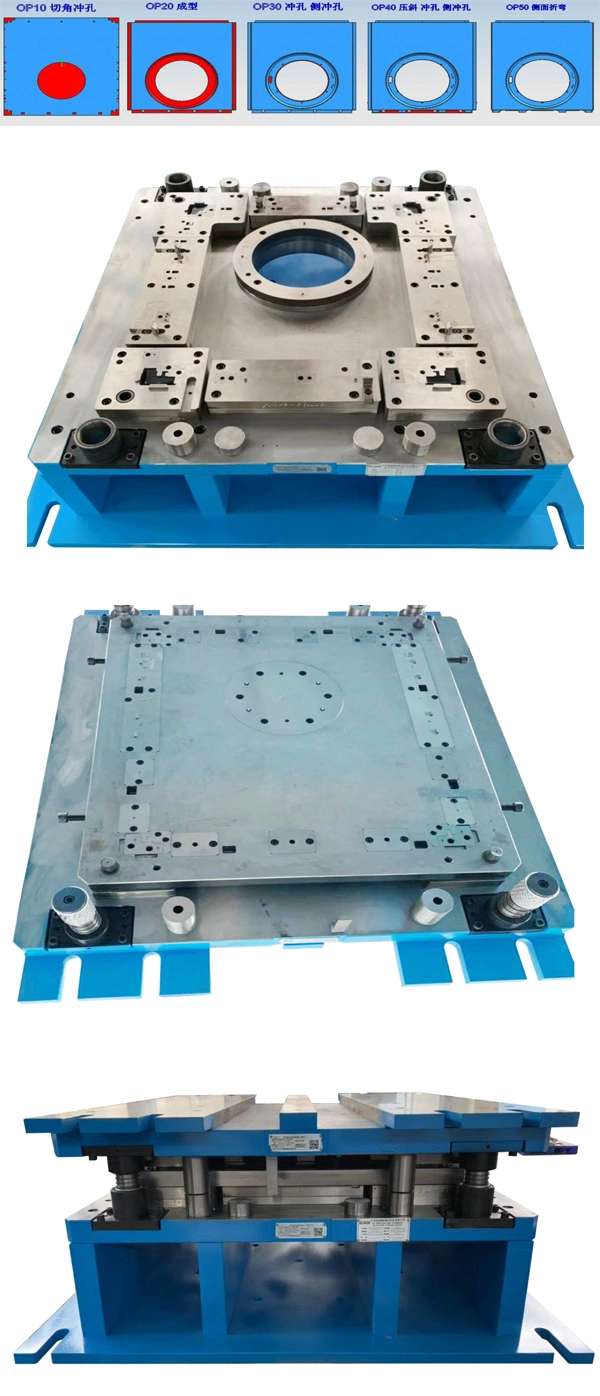
Project Description | |
project Name | Dryer Tools For Drum front Panel |
Mould Modes | Single Process Stamping die |
This Process | OP01--Conner Cutting And Punching |
Production Application | White Household Appliances Dryer Machine |
Metal Sheet Material | DX53D+Z 0.8mm |
Mould Material | V8, ASP60, P20, ASSAB88, XW-42, SKD11, DC53, CR12MOV, AMPCO25 |
Mould Base | SD, LKM Standard, HASCO Standard, Self-made, etc. |
Shut Height | 540mm |
Mould size | 1340*1290*540mm |
Mould weight | 2655kg |
Facility | 300T Punching Machine |
Mould Life | 500000 shots |
Drawing Format | DWG, STP, STEP, X_T, IGES, PDF |
Design Software | Auto CAD, UG |
Trade terms | FOB (Shanghai), CIF |
Payment Terms | T/T, Trade Assurance |
Mould Leadtime | Generally 6~8 weeks (as per actual situation) |
Quality management system | ISO9001:2015 |
--------------------------------------------------------------
ABOUT US
We are manufacturer which can provide the whole line solution including power press, feeder and decoiler, mould, Iron-hand,etc.
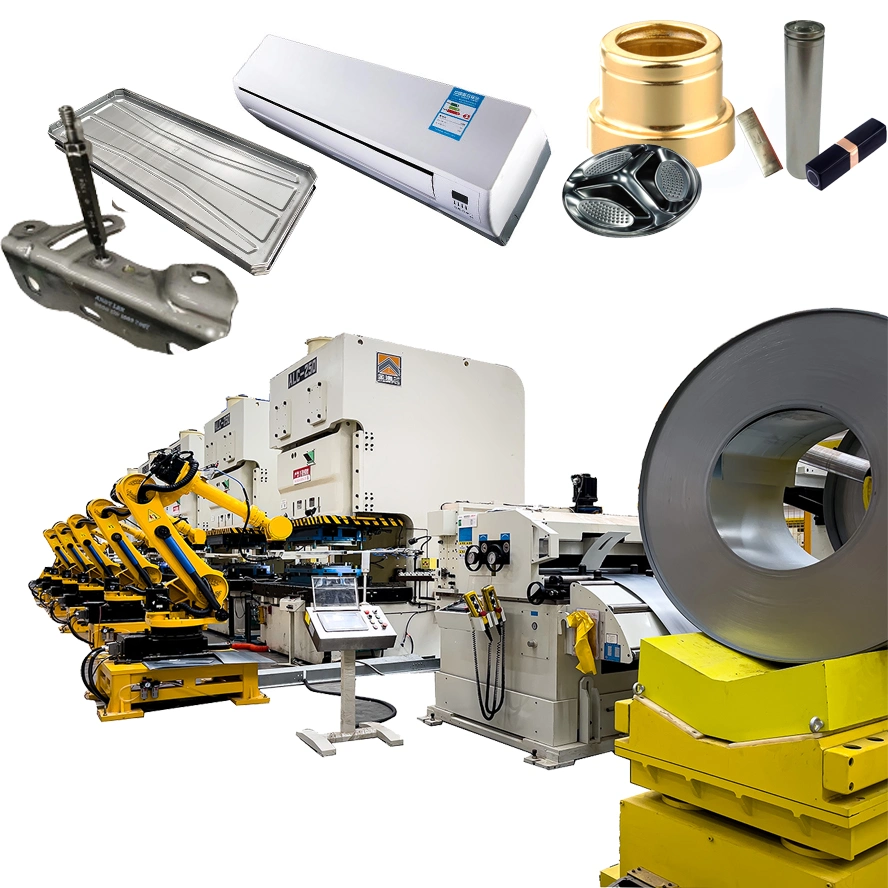
-Transfer system
-Robot
-Tools/Molds/Progressive die
- Production line complete solution
-Filed service /On line service
Mold Design& Manufacturing
The power press stamping molds/tools are including:
1. progressive die,
2. Stage mold (single stage mold),
3. Transfer mold (with transfer system)
What is the difference between progessive die, stage mold and transfer mold?
Continuous die (also known as progressive die, step die) refers to the press in a stroke, in turn in several different positions, at the same time to complete a number of procedures of the die. Blanking parts are gradually formed in the continuous die, continuous forming is a process method of process concentration, can make the edge cutting, incision, groove cutting, punching, plastic deformation, blanking and other processes in a mold to complete. According to the actual needs of stamping parts, according to a certain order arranged a number of stamping processes (called in the progressive die station) for continuous stamping. It can not only complete the blanking process, but also complete the forming process, and even the assembly process, many complex stamping parts that need multi-process stamping can be completely formed on a die, which provides favorable conditions for high-speed automatic stamping. It can be seen that the continuous die is a kind of punching die with many working stations and high efficiency.
Engineering mould (single working procedure mold/ single stage mold), is a single working position, single working procedure mould.It is characterized by a simple mold structure, the need for artificial or robotic arm assistance;So the relative production efficiency is low, mainly used for batch is not large, precision requirements are not high workpiece production.Due to the low cost of the engineering mould and the low requirement on the tonnage of the punch press, the engineering mould scheme is often preferred when making the mould scheme. However, with the continuous cost rising, the engineering mould will be gradually replaced by the continuous mould or transfer mould.
Multi-station transfer mold, generally refers to the use of special multi-station punch, by a number of engineering mold with a certain process connection according to the process sequence installation, a kind of mold delivered by the manipulator. The most important characteristics of the multi-station transfer die (1) in the use of multi-station punch;(2) Each station is a complete engineering model to complete a specific process. Each engineering mold (single station-mold) has a certain connection, each station mold can be adjusted independently, and the adjustment is generally not restricted by the front and back mold;(3) transmission mode: mechanical hand delivery.
Regular Mold Manufacturing parameters
Product Name | Precision metal progressive stamping dieprecision metal progressive stamping die |
Material | SKD11,D9, Tungsten steel, Cr12 Mov |
Standard | DIN GB ISO JIS BA ANSI |
Design file format | dwg, dxf, step, x_t, top, igs |
Tooling manufacturing cycle | 3 weeks to 10 weeks |
Forming way | Punching, blanking, bending, burning, deep drawing, forming, etc |
Stamping parts | Aluminum, phosphor bronze,stainless steel,steel,alloy,copper,plastic etc |
Parts machining equipment | Hot galvanized,Polish,Anodize,Sand blasting,Powder coating,Vacuum Plating,Nickel, Zinc, Chorme,Tin, Silver plating, gold-plated,imitation gold-plated,etc |
Our produced products
Punching machine
KINGLAN press machines models
About US
Our brand is KINGLAN, the main products we producing are pneumatic presses (20-2400T) and progressive die, laser tube cutting machine, feeder machine, and so on, which mostly used for metal piercing,drawing,forming,cutting,levelling and blanking.KINGLAN Company has more than 300 employees, and the college education accounted for 70%. In 2012, the company increased the investment of USD 100 million on the original basis, which
enhanced the competitiveness, so that the products reached the top level in China. After
continuous development, our current power press are also excellent in the world. Our
technologists come from Japan,Germany, and Taiwan. At present,our quality customers includ GM, GREE,Ford,ZOTYEAUTO,VW,Midea,Vanward,Aux,ect.
We can provide the whole line solution including power press, feeder and decoiler, mould, Iron-hand,etc.
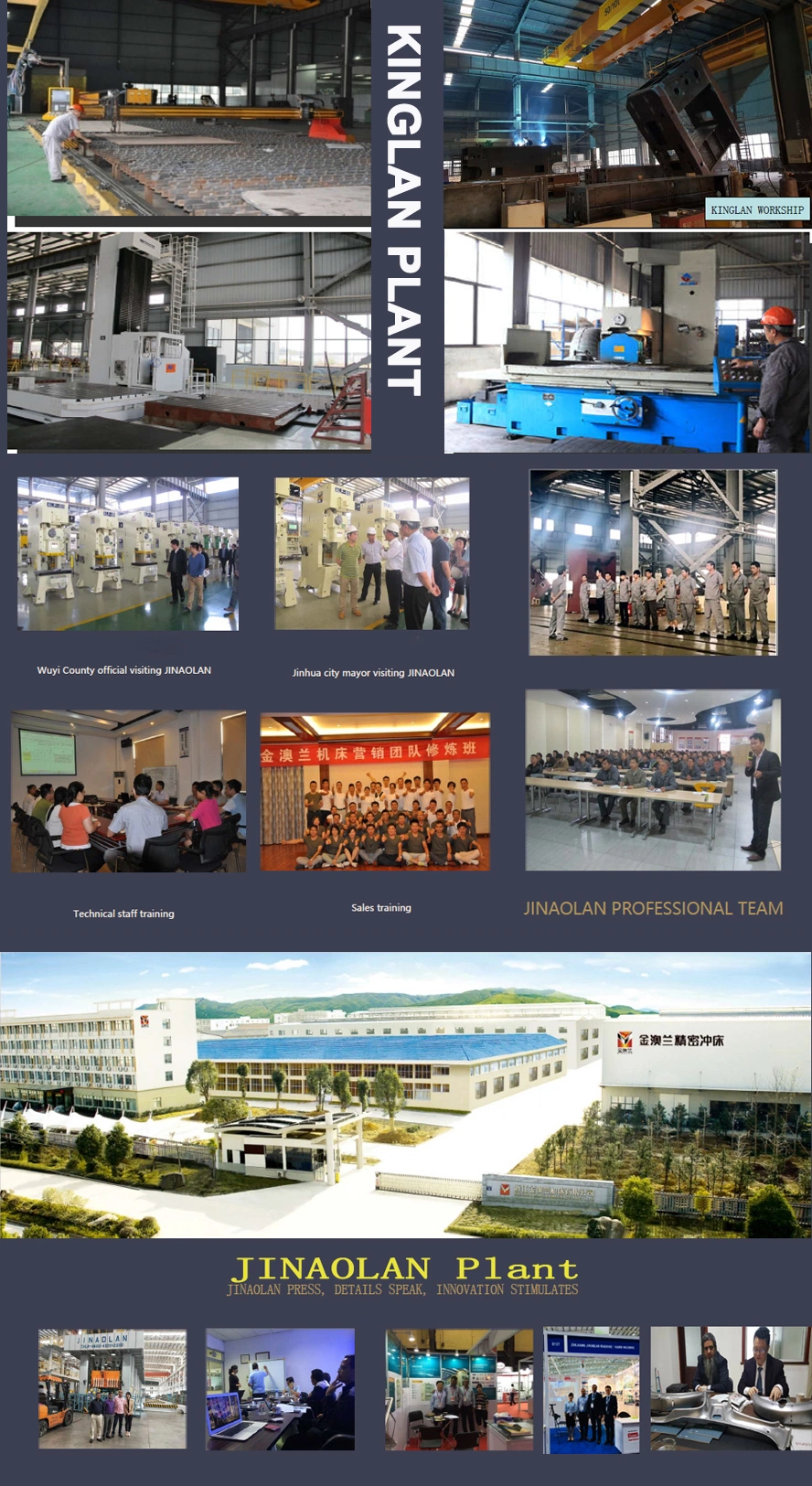
Our technologists come from Japan,Germany, and Taiwan. At present,our quality customers includ GM, GREE,Ford,ZOTYEAUTO,VW,Midea,Vanward,Aux,ect.
Power presses are used to shear, punch, form, or assemble metals or other materials by using tools or dies attached to slides or rams. Used in large industries for heavy operations, power presses can be powered by pneumatic, hydraulic or mechanical means.
In all our years of manufacturing quality power presses and other power press products, we have made it our goal to put the customer first. We believe in offering the right solution to meet your needs, whether it is having the right parts to fix your existing machines, the presses you need at an affordable price, or the ongoing support to keep your machines in top condition.
Our goal is to provide our customers with the highest level of quality, whether it is in our power presses and other press designs, or in our customer service dealings with each customer. We have been in business for 20years, which makes us uniquely suited to meet the needs of our varied customers. Contact us today to learn more! Thanks!